August - December 2018
For my senior project at USC, my team chose to work on a project that would have potential applications in the medical robotics field. We incorporated a phenomenon called particle jamming, which allows for the effective gripping of objects.
Background
Gripping objects is a crucial task in both manufacturing and medical applications. Hard end effector robots can pick up heavy objects but have limitations with irregular shapes, while soft end effector robots can pick up various shapes but with less strength.
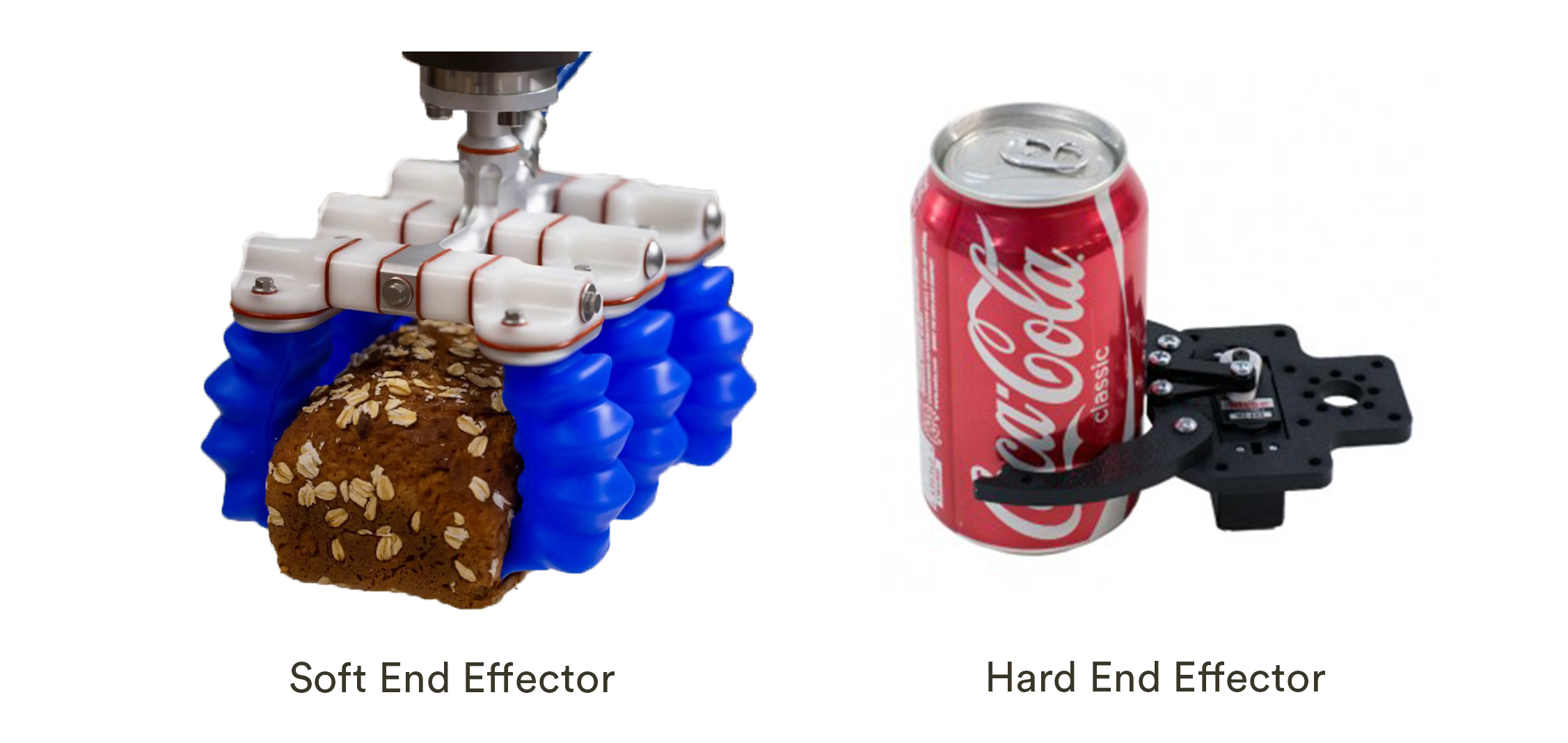
Soft end effectors (powered by air) can only pick up lighter objects with various shapes, while hard end effectors can pick up soda cans and other heavier objects but only with a uniform shape.
A particle-jamming gripper combines the two with flexibility in shape and size — a gripper is a membrane filled with grains and attached to a vacuum (in this case, we used a balloon filled with salt and coffee grounds). It is able to form over any irregularly-shaped object, and when the vacuum is pulled, the air is removed from the gripper, and the grains "pack" and deform around the object to can pick it up with a high holding force.
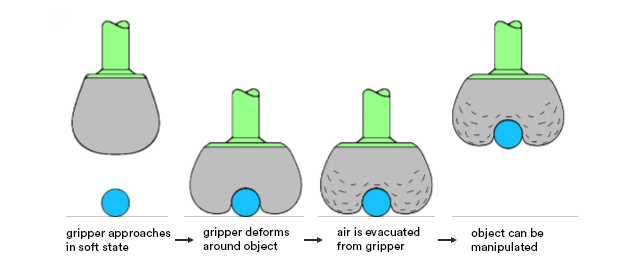
Source: Kurzweil, a gripper using soft robotics, 2014
Setup
We needed to find a way to quantify the effectiveness of the particle-jamming gripper, so we created a setup of two particle-jamming grippers. We machined funnel-shaped aluminum grippers and attached them via aluminum links to an 80/20 frame. We placed grain-filled balloons into each gripper (the grains used were salt, coffee grounds, turbinado sugar, and rice) and attached them to a vacuum setup. We then placed 3D-printed test objects between the grippers and attached weights onto the object until it fell.
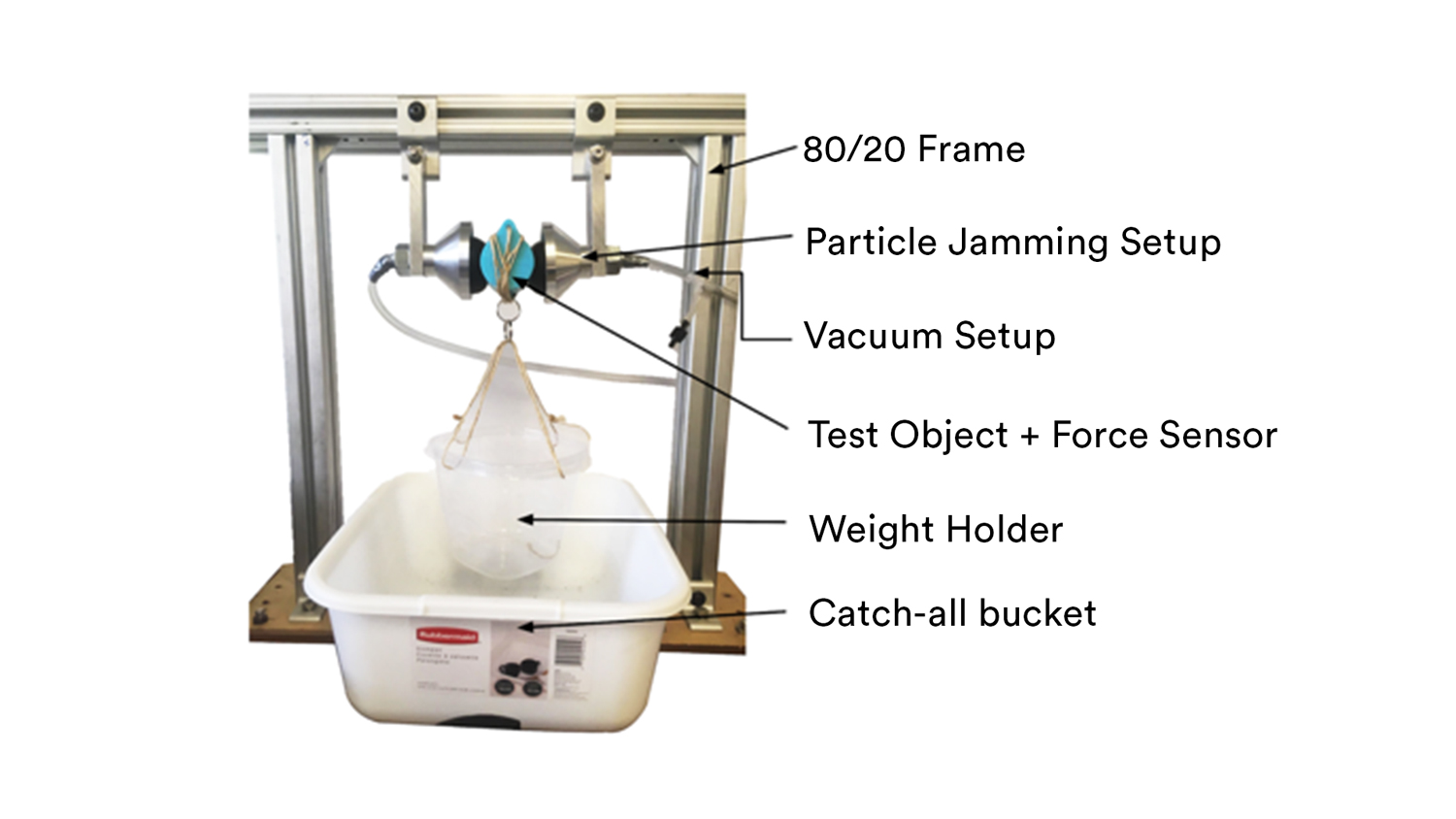
Aside from taking test data and building the setup, I focused on the prototyping development of the funnel grippers. I started by making initial drawings to understand the parts needed to attach the funnel to the vacuum and the 80/20 frame, made and refined the CAD models, then finally machined the funnels on aluminum 6061.
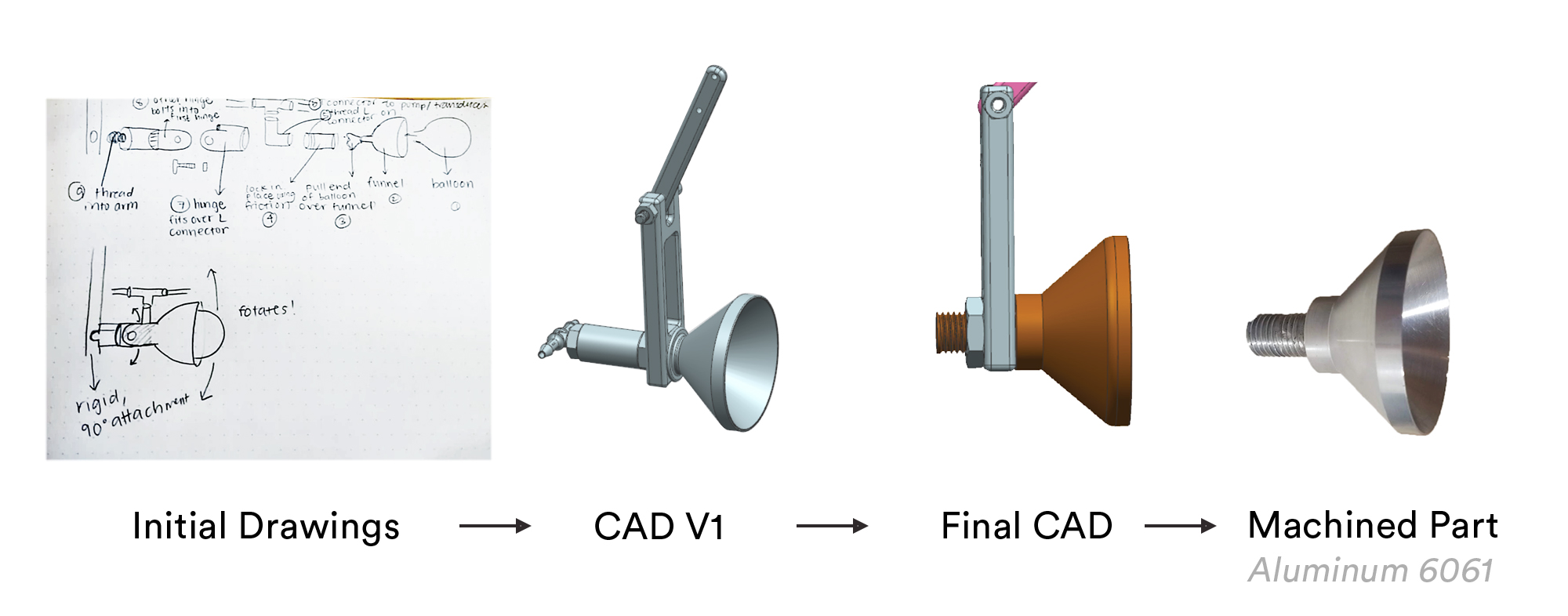
In addition to prototyping, I also managed the team schedule for our team of four, recording our weekly progress and keeping track of our semester-long timeline using a Gantt Chart. With four months to complete our project, it was crucial to keep track of our progress to hit deadlines and get parts machined quickly. I checked in on our team's progress and tweaked the schedule as we went.
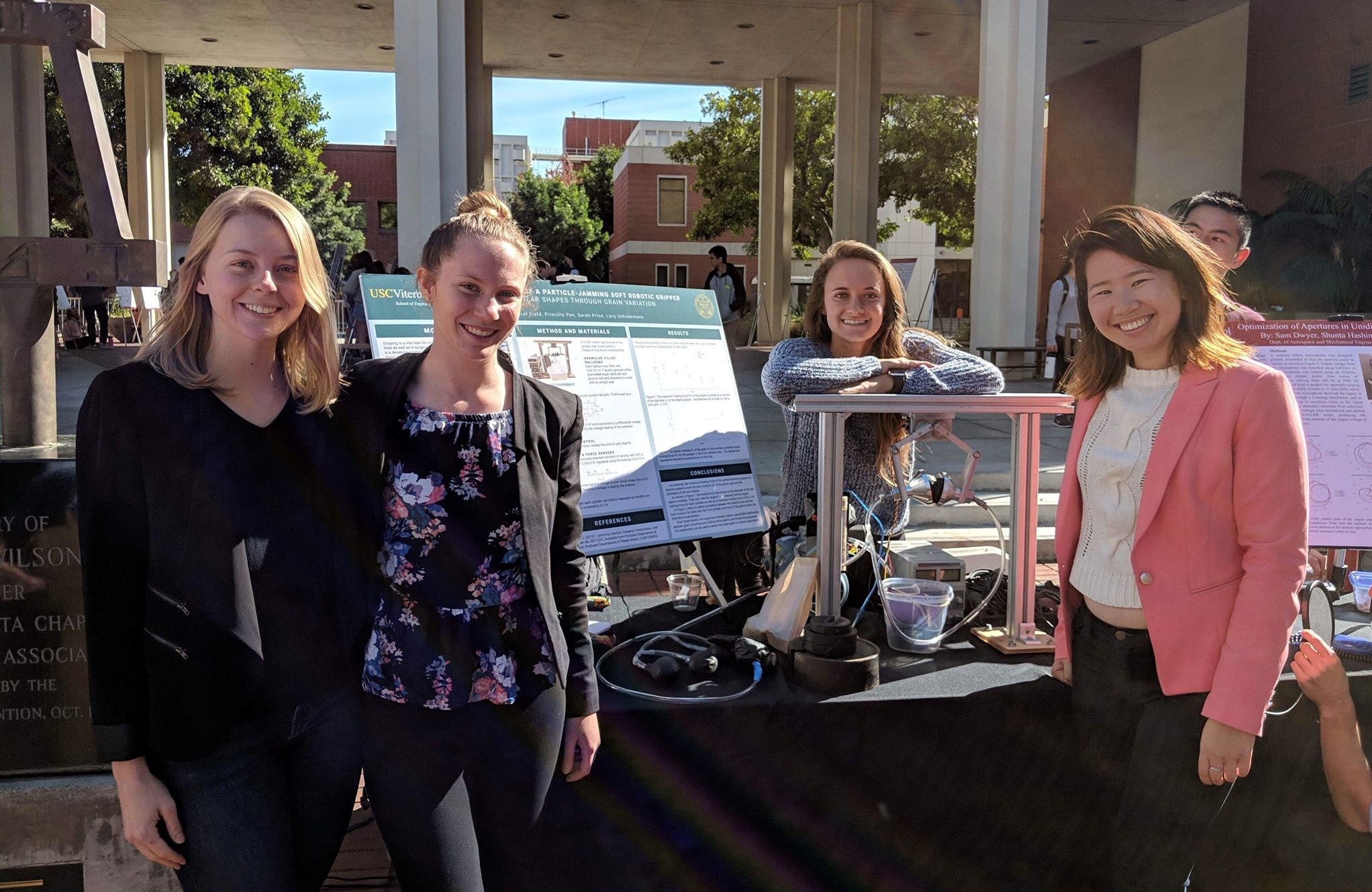
My senior project team at our final presentation.